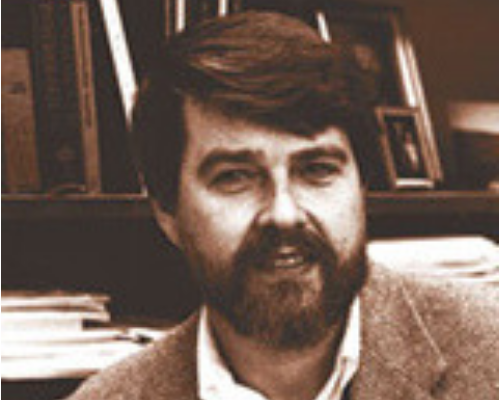
History
In March 2010 the Rumelhart Prize selection committee and the Glushko-Samuelson Foundation set out to create a bronze medallion that would be awarded to past, present and future winners. David T. Waller, a renowned artist and sculptor based in London, was commissioned to design the medal. Using photos obtained from Rumelhart’s former students and collaborators the artist fused the scientist’s memorable features with his customary pose before answering a question where he would caress his beard with his fingers. The design for reverse side of the medallion was selected from 40 original drawings by the artist. The final choice shows two heads in profile looking at one another into the center. Waves and flowing lines connect the heads to represent communication and understanding. In the centre is a version of the ‘Psy’ symbol which is harmonized with more curves or waves recognizable in graphs and tables showing results of surveys and experiments. Prof. Rachel Wu, cognitive scientist and artist, provided invaluable assistance to the design effort and presentation.
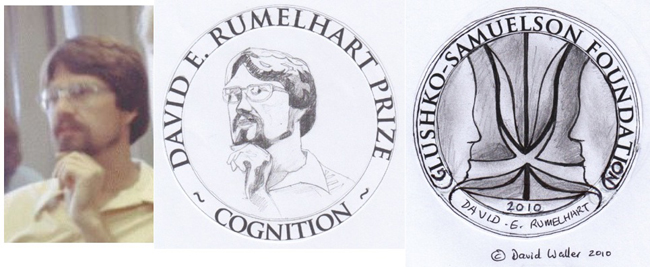
Sketches
Reference picture of David E. Rumelhart and final sketches of the front and back of the medallion.
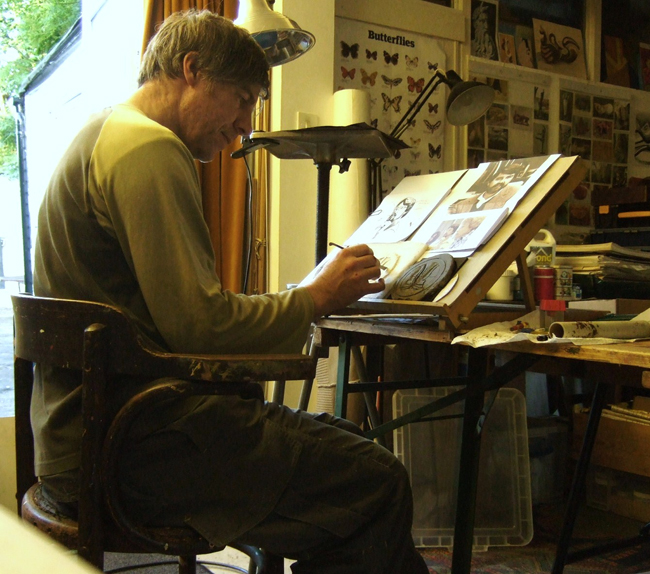
Making the original
Artist David T. Waller in his studio using the references to make the original wax model (front and back).
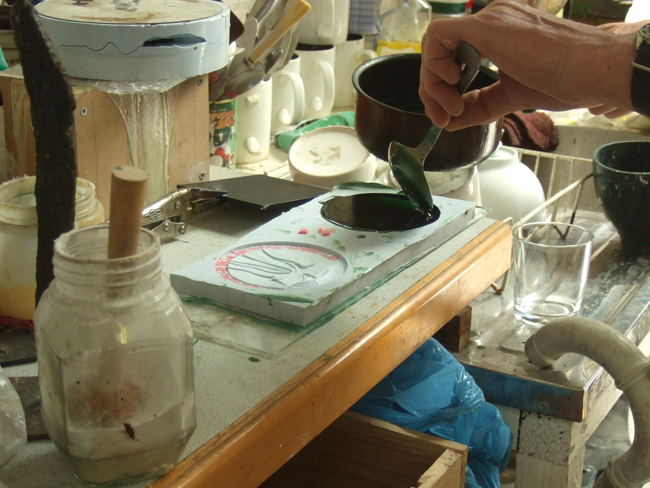
Silicon Casting
The two pieces then are cast into silicon rubber molds, which are used to create exact wax copies of the original.
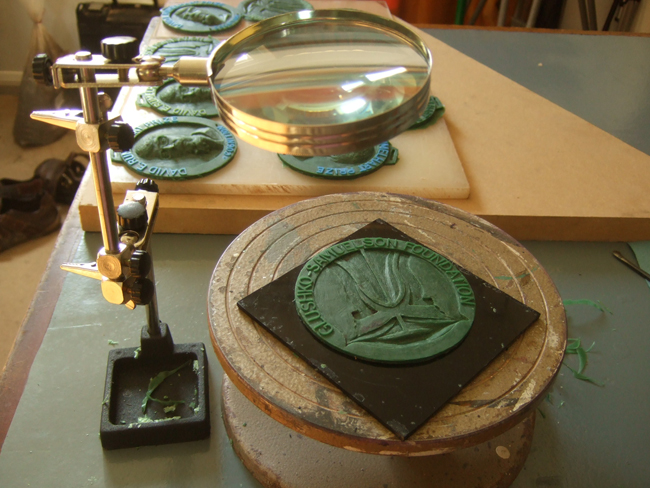
Detailing
The wax copies (front and back of the medallion) are carefully refined. Every detail in the final wax copy will be replicated in bronze. Therefore, there needs to be the same number of wax copies as there are final bronze medallions.
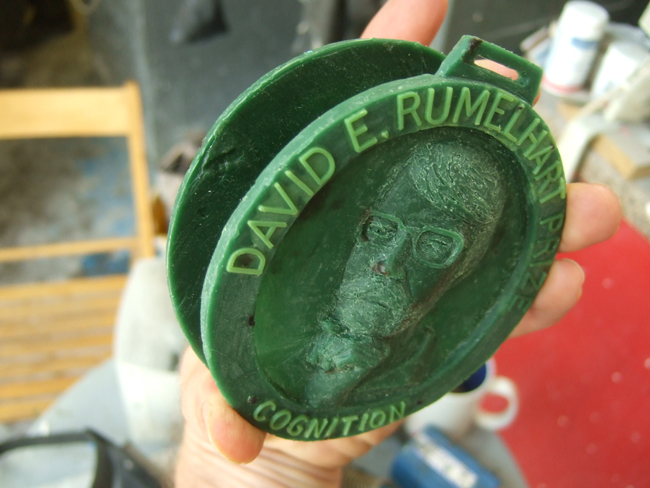
Assembly
The front and back of the prize winner’s medallion is assembled. Each wax copy is then carefully invested in a special ceramic shell.
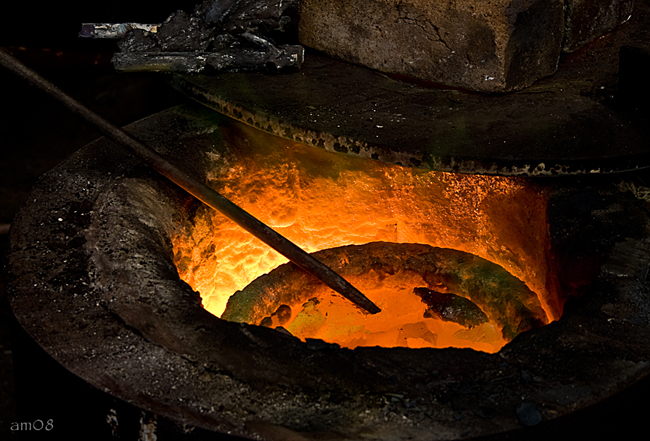
Wax casting
Once heated, the wax flows out of the shell. The silicon bronze then is melted in the crucible to above 1000°C and poured into the shell in a process known as “lost wax casting”.
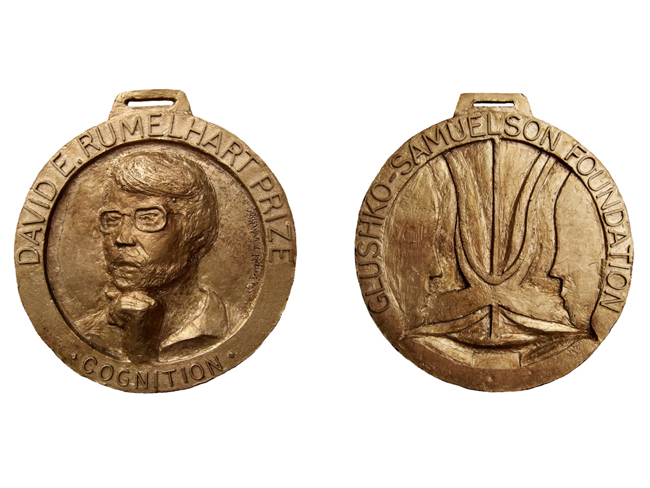
Chasing and Fettling
The bronze pieces are cleaned and refined in a process known as chasing and fettling to produce the honey-colored medallion.
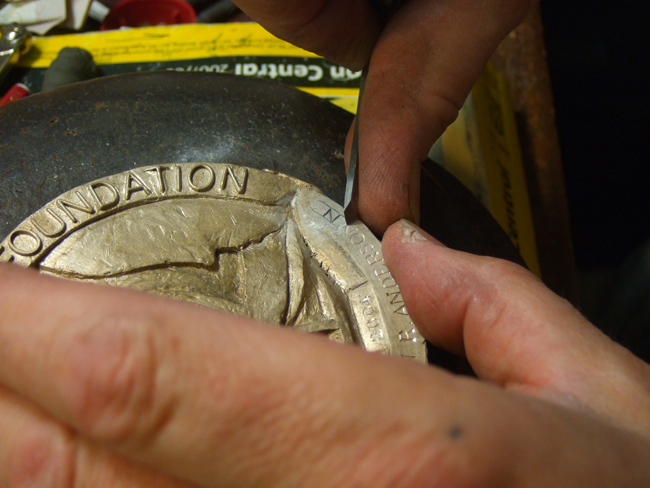
Engraving
The medallions are then shipped to the engraver, who hand-carves the name of the recipient and year of the award.
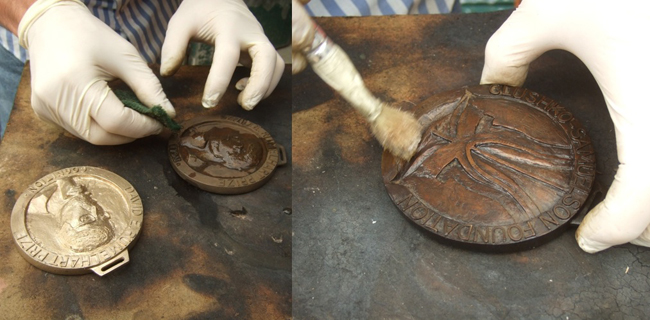
Patination
The medallion is returned to the foundry to be patinated. Chemicals and water are brushed onto the heated bronze. Finally, the neutral wax is applied with a brush to give it an antique leather-colored appearance.
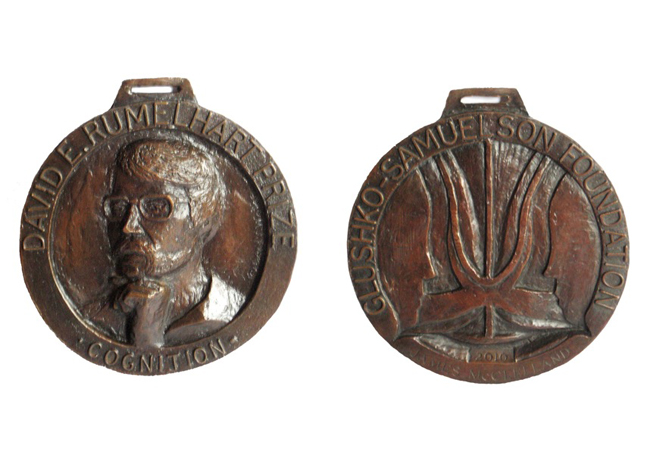
Finished Medal
The final bronze medallion is ready to be packaged. A blue ribbon is attached and the medallion is presented to the recipient in a special royal blue box lined with satin.